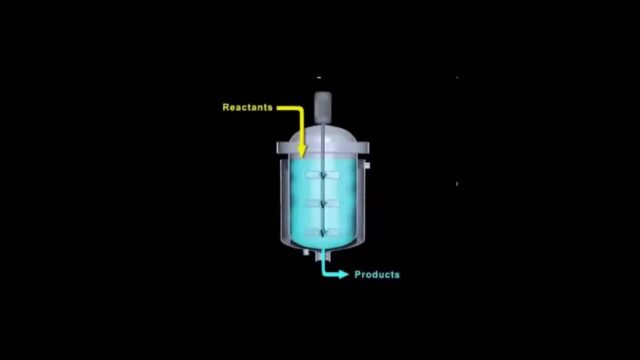
In the realm of chemical engineering, reactors are the virtuoso instruments that orchestrate the intricate dance of molecules, orchestrating their transformation into new compounds. Among these reactors, the Continuous Stirred-Tank Reactor, or CSTR, stands as a maestro in facilitating chemical reactions through its unique design and operation.
This article delves into the heart of CSTR reactors, unraveling their inner workings, design considerations, advantages, and applications. Let’s embark on a journey to explore the symphony of chemical transformation that takes place within the realm of CSTR reactors.
Batch Reactor vs CSTR
Before delving into the intricacies of CSTRs, let’s take a moment to juxtapose them with their counterpart – the Batch Reactor. Unlike the latter, which manages reactions in isolated batches, the CSTR functions seamlessly in a perpetual flow, enabling a constant influx of reactants and a continuous efflux of products. This pivotal differentiation engenders an unbroken stream of reactions within the CSTR, rendering it indispensable for applications necessitating unwavering production rates.
Design
At the core of what makes the CSTR impressive is how it’s built. It has a special tank that gets stirred, helping all the ingredients mix really well and spread out evenly. This stirring keeps the ingredients always touching each other, which helps the reactions happen faster.
Now, let’s think about how big the tank needs to be to get the results we want. This is where the algebraic rate equation comes in. It’s like a special formula that takes into account how fast the reaction happens, how much of the ingredients there are, and how the reaction works. Engineers use this formula to figure out how big the tank should be so that we get the exact results we’re looking for.
PFR vs CSTR
While the CSTR has its merits, it’s important to mention its counterpart, the Plug Flow Reactor (PFR), which operates with minimal mixing and resembles a flowing pipe. The key difference lies in the concentration profiles; CSTRs exhibit more uniform concentrations due to mixing, whereas PFRs maintain gradients along their length. Depending on the reaction characteristics and desired outcomes, engineers choose between these reactors to strike a balance between conversion and selectivity.
Advantages and Disadvantages
Every performance has its nuances, and the CSTR is no exception. Its strengths lie in its simplicity, adaptability to various reactions, and effective heat management due to the constant mixing. However, its limitations include reduced selectivity for consecutive reactions and difficulties in achieving high conversions for reversible reactions. Balancing these advantages and disadvantages guides engineers in selecting the right reactor for the symphony of chemical reactions they intend to conduct.
CSTR Residence Time Distribution (RTD)
Imagine a symphony hall where different seats experience variations in sound quality. Similarly, within a CSTR, there are differences in residence times for different molecules due to varying flow patterns. The Residence Time Distribution (RTD) characterizes these discrepancies, providing insights into reactor behavior. Engineers analyze RTD curves to optimize reactor performance, ensuring that each molecule has an opportunity to partake in the chemical melody.
Modeling and Simulation
In the digital age, simulating reactor performances has become indispensable. Engineers employ mathematical models to predict how a CSTR will behave under specific conditions. These models take into account factors such as reaction kinetics, heat transfer, and mass transfer. By feeding these models with data, engineers fine-tune operating parameters to achieve desired outcomes without the need for extensive trial and error.
PAT Integration
Process Analytical Technology (PAT) acts as the conductor’s baton, ensuring precision and control in chemical processes. Integrating PAT tools into CSTR operations enables real-time monitoring of parameters such as temperature, pressure, and reactant concentrations. This live feedback loop empowers operators to make immediate adjustments, maintaining optimal conditions and enhancing both safety and efficiency in the reactor’s performance.
Industry Applications
Pharmaceuticals
- CSTRs used in drug synthesis and manufacturing.
- Ensures controlled and consistent production of pharmaceutical compounds.
Petrochemicals
- Vital for producing various petrochemical products.
- Plays a role in refining and transforming raw materials into valuable chemicals.
Specialty Chemicals
- Used in manufacturing specialty chemicals and intermediates.
- Offers adaptability to a wide range of reactions.
FAQs
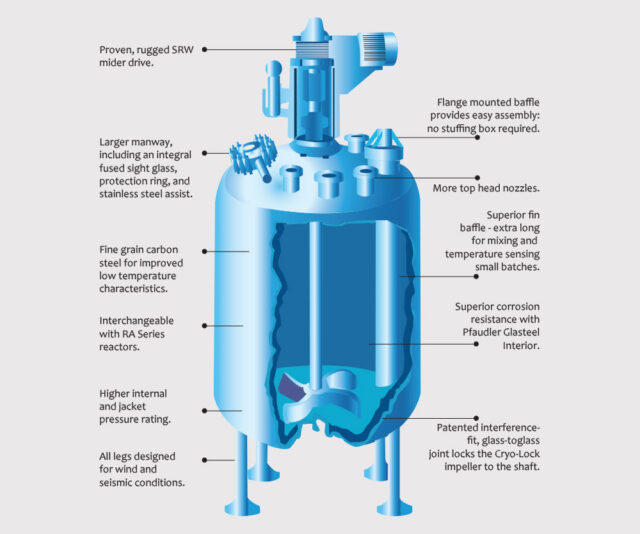
Q1: What is a CSTR reactor?
A Continuous Stirred-Tank Reactor is a type of chemical reactor that operates in a continuous flow manner, allowing for a constant influx of reactants and efflux of products.
Q2: How is the reactor volume determined for a CSTR?
The reactor volume required for a CSTR is determined using the algebraic rate equation, which takes into account reaction rates, reactant concentrations, and reaction orders.
Q3: What is the advantage of a CSTR’s constant mixing?
Constant mixing in a CSTR ensures uniform reactant distribution, promoting efficient reaction kinetics and effective heat management.
Q4: How does it differ from a PFR?
Unlike a CSTR, a PFR operates with minimal mixing and maintains concentration gradients along its length.
Q5: What is the significance of Residence Time Distribution (RTD)?
RTD characterizes differences in residence times within a CSTR, providing insights into reactor behavior and helping optimize performance.