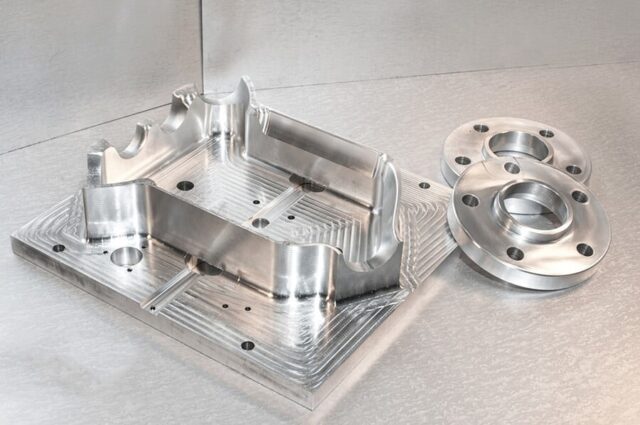
Choosing between cast and machined aluminum can be a tricky decision. Both materials offer distinct advantages and potential drawbacks, making the choice dependent on the specific needs of your project.
In this blog post, we’ll break down the differences, benefits, and potential regrets associated with each type, helping you make an informed decision that aligns with your goals. Which to choose; cast vs machined aluminum?
What is Cast Aluminum?
Cast aluminum is produced by melting aluminum and pouring it into a mold. This process allows for complex shapes and intricate designs, making it ideal for parts that need to be manufactured in large quantities with consistent properties.
Advantages
- Cost-effective for large runs ─ Casting is cost-effective, especially for large production runs. The initial cost of creating molds can be high, but it pays off when producing thousands of parts.
- Complex geometries ─ The casting process allows for the creation of complex shapes that would be difficult or impossible to achieve with machining.
- Uniform properties ─ Cast aluminum tends to have uniform properties throughout the part, which can be beneficial for certain applications.
Disadvantages
- Porosity issues ─ Casting can sometimes result in porosity, where small air bubbles are trapped in the material, leading to potential weak spots.
- Surface finish ─ Cast parts often require additional finishing processes to achieve a smooth surface, which can add to the overall cost and time.
- Strength limitations ─ Cast aluminum generally has lower tensile strength compared to machined aluminum, making it less suitable for high-stress applications.
Machined Aluminum
Machined aluminum involves taking a solid block of aluminum and removing material to create the desired shape. This process is highly precise and allows for excellent control over the final product’s dimensions and properties.
Advantages
- High precision ─ Machining allows for extremely tight tolerances and high precision, making it ideal for parts that require exact specifications.
- Better surface finish ─ Machined parts typically have a superior surface finish right out of the process, often requiring little to no additional finishing.
- Stronger parts ─ Since machined parts are cut from a solid block, they tend to have higher tensile strength and are better suited for high-stress applications.
Disadvantages
- Higher cost for low volumes ─ Machining can be expensive, especially for low-volume production runs, due to the time and labor involved.
- Material waste ─ The machining process involves removing material, which can lead to significant waste, especially with complex parts.
- Longer lead times ─ Machining complex parts can take longer compared to casting, potentially leading to longer lead times.
How to Choose
When deciding between cast and machined aluminum, consider the following factors:
1. Production Volume
- High volume ─ If you need a large number of parts, casting is usually more cost-effective due to the lower per-unit cost once the mold is created.
- Low volume ─ For small production runs or prototypes, machining might be more economical despite the higher per-unit cost.
2. Part Complexity
Cast aluminum is better suited for complex shapes and intricate designs that would be difficult to achieve with machining.
Machined aluminum is ideal for parts with simple geometries that require high precision and tight tolerances.
3. Strength Requirements
If the part needs to withstand high stress or loads, machined aluminum is generally the better choice due to its superior strength.
For parts that don’t require high strength, cast aluminum can be a cost-effective and sufficient option.
4. Surface Finish
If a smooth surface finish is crucial, machined aluminum is the way to go as it typically requires less post-processing.
If surface finish is not a primary concern, casting might be more suitable, with any necessary finishing done afterward.
5. Budget and Lead Time
Consider the initial costs and the overall budget. Casting has higher upfront costs but lower per-unit costs for large runs, while machining can be more expensive per unit but might have lower initial costs.
Time Sensitivity
If lead time is a critical factor, machining can sometimes offer faster turnaround for complex parts, while casting might be quicker for simpler, high-volume parts.
In Summary
In the end, the decision boils down to what you value most in your project. Consider the trade-offs, evaluate your requirements, and you’ll be less likely to face regrets.