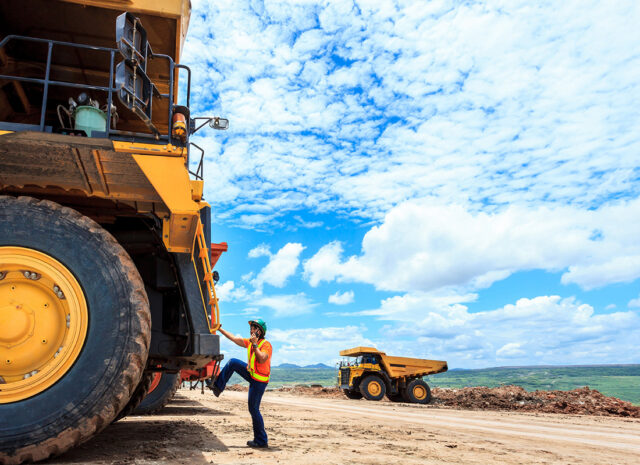
When it comes to monitoring and especially proper maintenance, the most crucial part is prevention, as everything else can be in vain if we don’t take all precaution measures in time. All of this is even more highlighted when we talk about heavy-duty equipment here, as even the smallest mistake can cause so many problems. Besides that, it will all get even more costly as necessarily repairs caused by negligence can really impact your budget and planning. Furthermore, if it has come to that point where you need to replace some part or repair it, it’s always preferable to go with a new part instead of picking the one that’s used just because it costs less.
Yes, it will cost less, but if we take a look at a bigger picture, eventually you will have to replace that part, so why pay double. Of course, it’s also about choosing the right company, the one with vast experience in the oil, mining, and construction industry, the one like https://sts-global.com/.
But, if you are more into tips for monitoring and maintenance of heavy-duty equipment, let’s check these five tips.
1. Keep all the documents
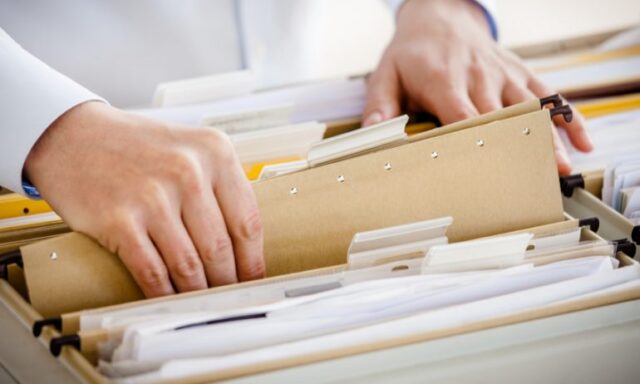
Many people are not aware of how important it is to keep all the documents about machine repairs and services in one place. Namely, these papers are of vast importance because of many factors, like knowing details in case of any malfunction, the order in which certain actions are needed, etc. It is crucial to have access to them at all times, and it is necessary because it will make the repairs and maintenance much easier, and what’s perhaps even more important, it will shorten the time spent on doing so.
In that way, you will always be able to check when was the last service, what was precisely done and fixed, and which part should be replaced soon as, after the service, you get detailed info about which the parts are good but will soon need replacing. Keeping all the papers can also be useful if we need to use the warranty because we will have written evidence that we can later show and prove that the machine is maintained in a proper way, but the breakage did occur.
2. Proper use is crucial
Regardless of what type of equipment we are talking about specifically, every maintenance tip starts with proper and adequate use, and the same rule applies to heavy-duty equipment. Most breakages on heavy-duty equipment occur because of the improper use of them due to poor training, lack of time, or some other reason. Because of that, it is crucial to train your workers to use the machines properly, or they will cause damages often, and repair costs will be pretty high in the end. Keep in mind that a good employee is a well-equipped employee, the one that has all the necessary tools, but the one that has vast knowledge and preferably experience working with this type of equipment as well.
It is also of vast importance to teach employees when to use which machine since trying to do something with the equipment not designed for that task will do more harm than good for sure. Of course, you should also teach them not to rush and try to do all of the work in one day because rushing makes them less careful and prone to mistakes. So, by setting certain rules regarding when and how some machines should be used, you will cut the expenses on the repairs.
3. Do not forget cleaning
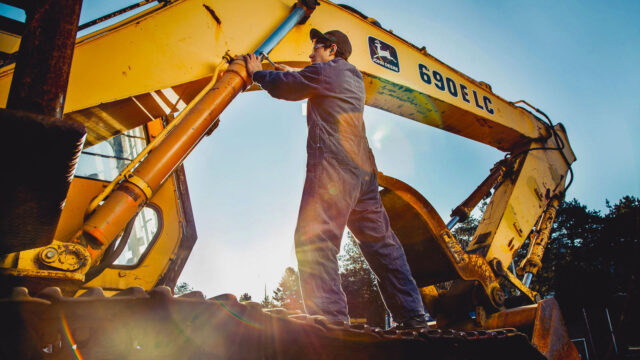
Now, this one should be something that’s not needed mentioning, but you would be surprised by how many problems and issues regarding heavy-duty equipment happen due to negligence. Namely, cleaning and checking whether everything about the machine is in proper order before you go home to relax is a must, as it’s the only way to be sure that the next day, nothing unforeseen will happen.
Although heavy-duty equipment might look like it does not need to be cleaned at all, in reality, things are much different, and it should be washed and cleaned like any other equipment or machine we use in our everyday life. The main reason for regular cleaning is that accumulated dirt can cause many malfunctions and breakages by blocking the moving part of the machine and stopping them from working. Besides that, cleaning is also a great way to search for other possible damages, and the detailed we are, the better it is. In the end, every machine looks much better and more professional when it is clean, so try to keep all of them as clean as they can be.
4. Fluids are very important
None of the heavy-duty machines can work without fluids, and it is up to us to keep them at the right level, or they can suffer unrepairable breakages. Overfilling fluids can cause damages, just like not filling them at all can, and because of that, it is crucial to be careful when filling them. It is also crucial to lubricate some parts of the machine properly and, in order to do that, you need to follow the manufacturer’s instructions, or the whole machine will not operate as smoothly as it should.
Of course, it is not enough only to keep fluids on the right level, as you need to think about their quality and use only high-quality products. The contaminated oil cannot provide the same quality as a new one, and because of that, it is necessary to do the checks and changes regularly.
5. Don’t forget about Hydraulics
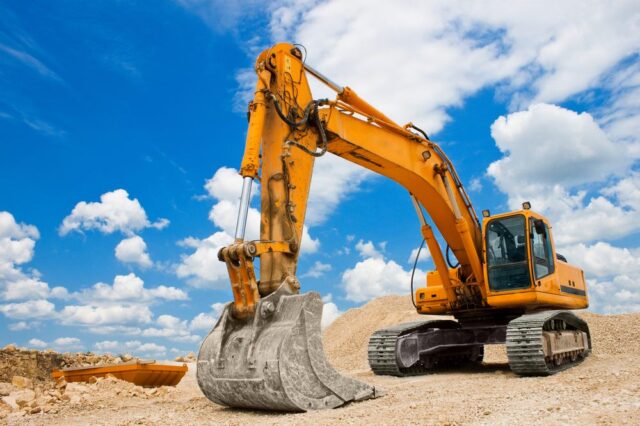
In addition to standard diesel engines that are used for movement and positioning, the most important segment of all machines is hydraulics, which is used for lifting and moving equipment. They are a very significant part of the machine, and it is necessary to take maximum care in order for everything to work properly. It is necessary to monitor the oil pressure in the system and periodically check the condition of hydraulic lines and hoses through which the oil passes under pressure.
Accidental rupture of the hose can lead to an accident due to the sudden release of the transferred load and even the injury of workers and machine operators. You should take even more care of it during the winter period due to the viscosity of the oil at low temperatures.