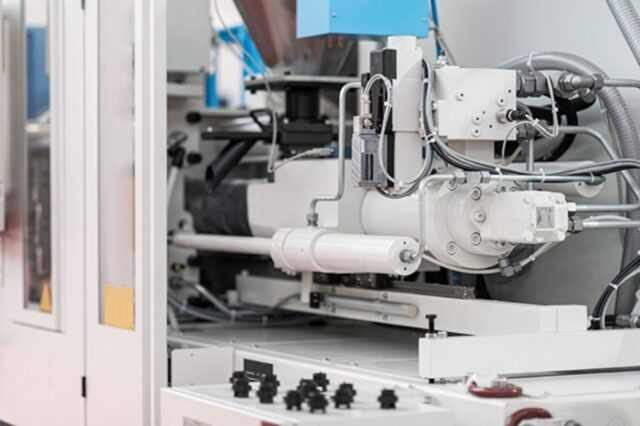
The injection molding method is a manufacturing technique that uses a hollow tool called a “mold” to manufacture parts of nearly every shape and size to produce plastic parts or pieces like toothbrushes, phone cases, light switches and other everyday use items.
The frame may be thought of as an empty framework into which raw materials, mostly plastics, will be poured in and then compacted under pressure. It is a common process in mass production in a lot of different industries.
This article will tell you all you need to know about this unique manufacturing process.
What Materials Can Be Used For Injection Molding?
The popularity of injection molding in the production of consumer goods and other items is due to the fact that any material can be molded into a ‘billet’ or ‘rod’.
All thermoplastics (like kydex), metals, and elastomers (such as rubber) can be injected. Plastics, however, are the most common material that’s used. Plastic is simple to melt and solidify. Plastics are available in a variety of properties, colors, and can be customized to almost any degree. Read here for more information on mixing colors.
What’s Injection Molding Used For?
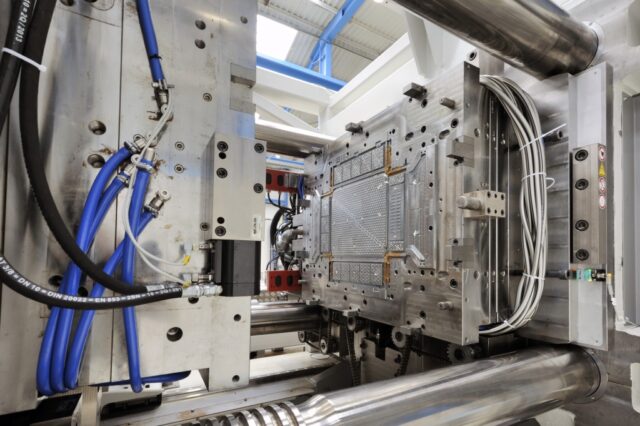
Injection molding is used in the production of just about any kind of consumer good. It’s especially important in injection blow molding and also injection stretch blow molding to create hollow products, such as bottles or large containers for shampoo, laundry detergent, etc. Injection molded parts can be found everywhere you look and are especially common in the automotive industry.
Injection molding is used to create a wide range of items, including toys, household goods, and even medical devices. Plastic caps, bottles, and containers are the most frequent components manufactured on a large scale using this technique.
Injection molding can be used for small devices that require precise fitting or big items like automobiles with many components, but in general, anything that needs a particular shape for efficient function can be made.
Molded goods can be found in a variety of forms, including milk cartons and yogurt cups. At first sight, it might not appear like it, but all of these items are manufactured using the same technique – injection molding!
Production Process Step By Step:
1. The Design
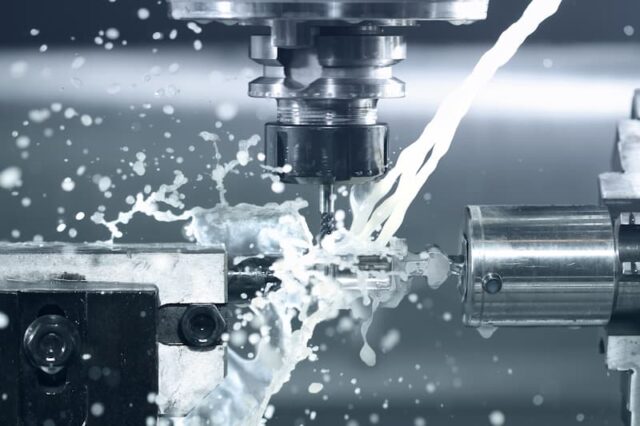
To manufacture an injection molded part, you must first draw it using sketches with computer aided design (CAD), or computer aided manufacturing (CAM). These files must then be converted from 2D data into 3D models/designs that CAD/CAM software can interpret. The molding machine will then create the design according to that software-designed workpiece.
2. Melding The Material & Injection
Plastic pellets are then fed into a hopper above the device, where they are melted and liquified before being sent through a lengthy barrel, or “injector,” into a mold. The mold, which is either aluminum or steel, must be carved out and comprise numerous sections as determined by the product being produced. The material takes the overall form of whatever cavity exists within the mold once it has been inserted.
3. Cooling Down
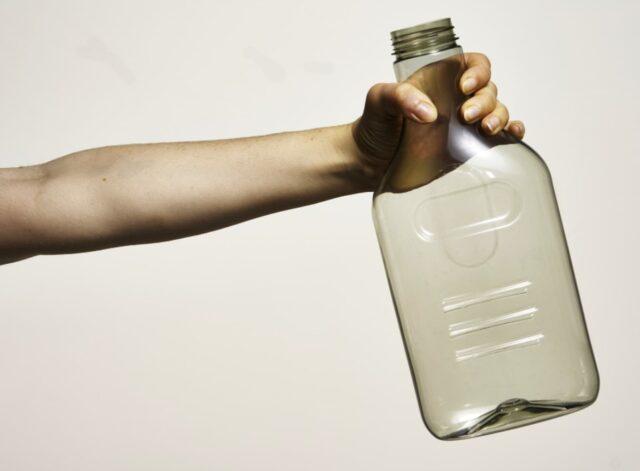
The liquid plastic hardens almost immediately when it comes into touch with the mold or sometimes needs a cooling system to harden. Before that pressure is used to eliminate all air bubbles and create a smooth surface.
4. Finish
After the plastic has completely cooled down and hardened it can be processed for the desired finishing touch.
What Are The Benefits Of Injection Molding?
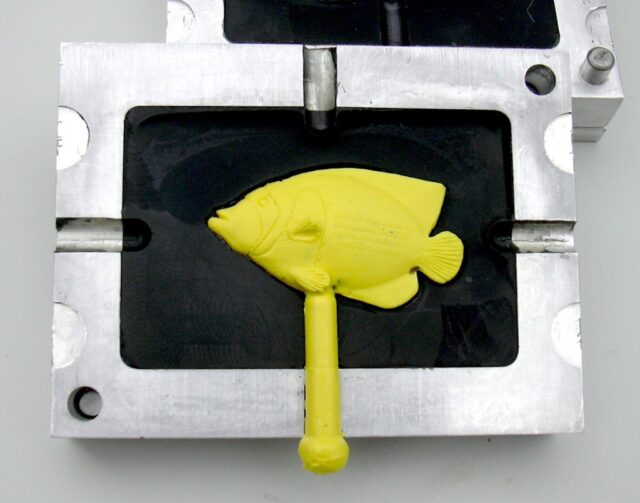
There are a number of reasons why injection molding has become one of the most used production processes in today’s industries. The benefits injection molding provides are:
1. Versatile
With injection molding, it is possible to create almost any shape and size. The only limitations depend on the type of mold used and the injection machine. With different types of injection molds, it is possible to produce plastic goods in almost any style or shape and color.
2. Durability
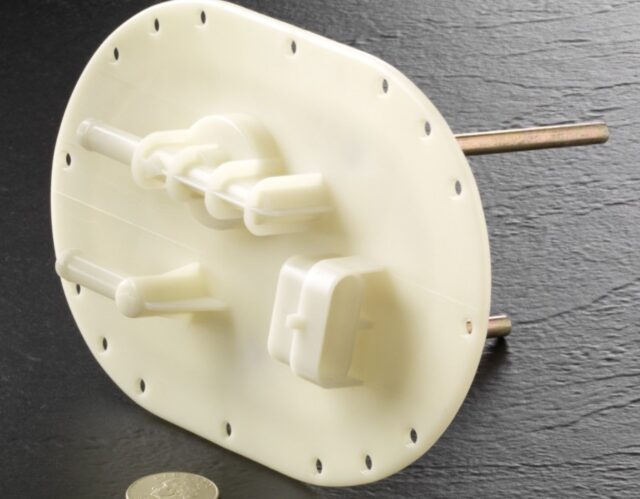
This process creates durable pieces. There is no need to worry about your injection molded plastic goods breaking or cracking.
3. Lower Costs
The injection molding process itself usually takes the least amount of time compared to other production processes, it is designed for mass production. It also does not require further steps like machining or welding, which makes it more cost-efficient.
4. Precision
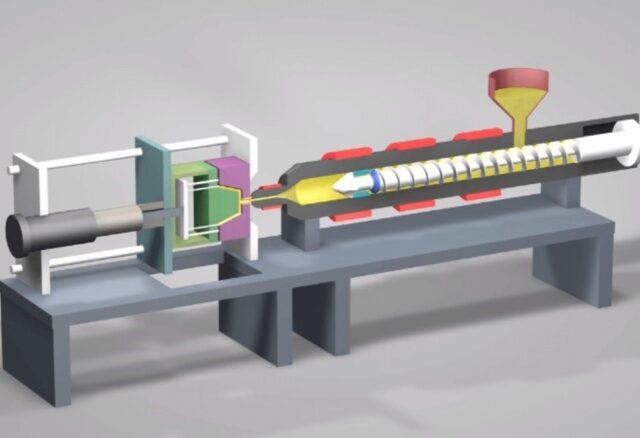
Injection Molding can produce very accurate workpieces that do not need any finish afterwards.
5. Manufacturing Convenience
Injection molding is convenient for manufacturing purposes because it can be set up automatically using an injection machine. This makes it possible to produce different goods all at one time, which lowers the total cost of production.
6. Large Production Capacity
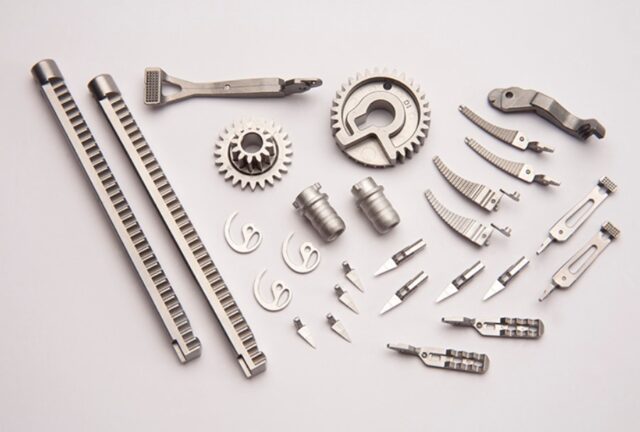
A lot of plastic products are made through injection molding including food containers. When it comes to quantity injection molding is the answer.
Injection molding is a great technology for finished production on a massive scale. It is also useful for finalized prototypes that are used for consumer and/or product testing.
Making Money With A Plastic Injection Mold
The plastic molding industry is growing exponentially. From pharmaceuticals to beverages, industrial sectors to food production, the market is estimated to be worth $475.9 billion by 2024.
A plastic injection molding service specializing in packaging is one of the fastest-growing sectors due to the demand for lightweight, flexible materials that are low-cost and moisture-resistant.
However, competition from overseas has made it increasingly difficult for domestic plastic injection molding businesses to survive. To succeed in the plastic molding industry we recommend:
Research Demand For Plastic Molded Parts
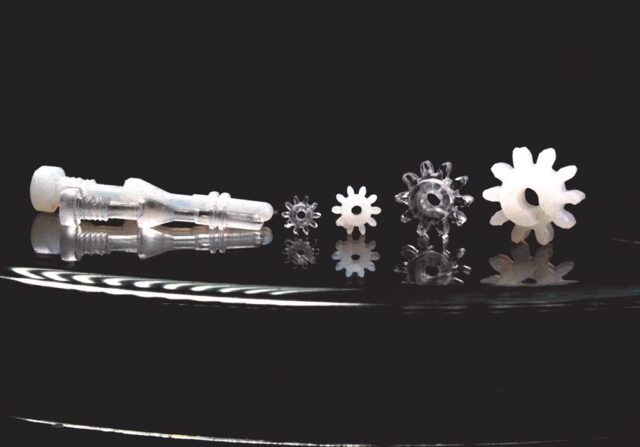
Any new company requires a business plan, but it’s especially crucial if you want to make money with injection molding. The best way to evaluate demand is to immerse yourself in networking and identifying why a potential customer may switch suppliers.
Investing Wisely In Injection Molding Equipment
The next factor is your equipment. Undoubtedly, to compete with existing manufacturers, you will need to invest in good-quality machinery. You will need molding equipment, material handling tools, plastic dryers, inspection machinery, robotics, and overhead cranes to get started. Keep in mind that there is little merit in over-investing in high-value machinery you can’t afford, even if it does represent the most innovative option on the market.
Identify Your Plastic Injection Molding Niche
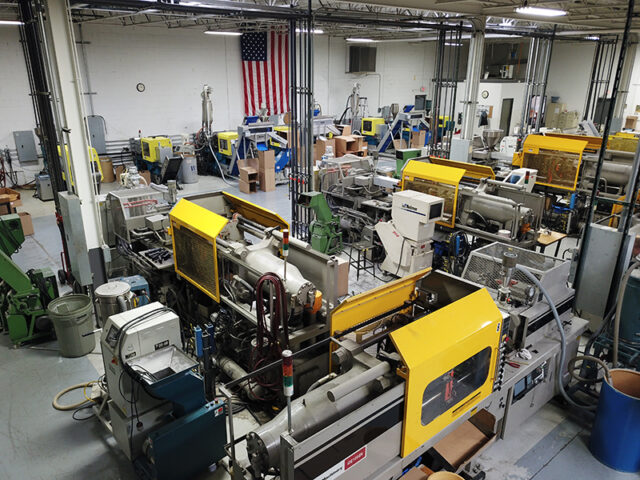
Finally, it pays to have a USP that differentiates your business offering from the competition. While you probably cannot compete on price with large scale manufacturers, no business is a comprehensive leader in every aspect of their trade, and so as a new business, you need to identify areas where you have a specialty.
The plastic injection molding industry is a challenging field to enter, but with a growing market, it might be worth your investment. And with proper research, wise investments, and specialized expertise, you will become a competitive business in the field.